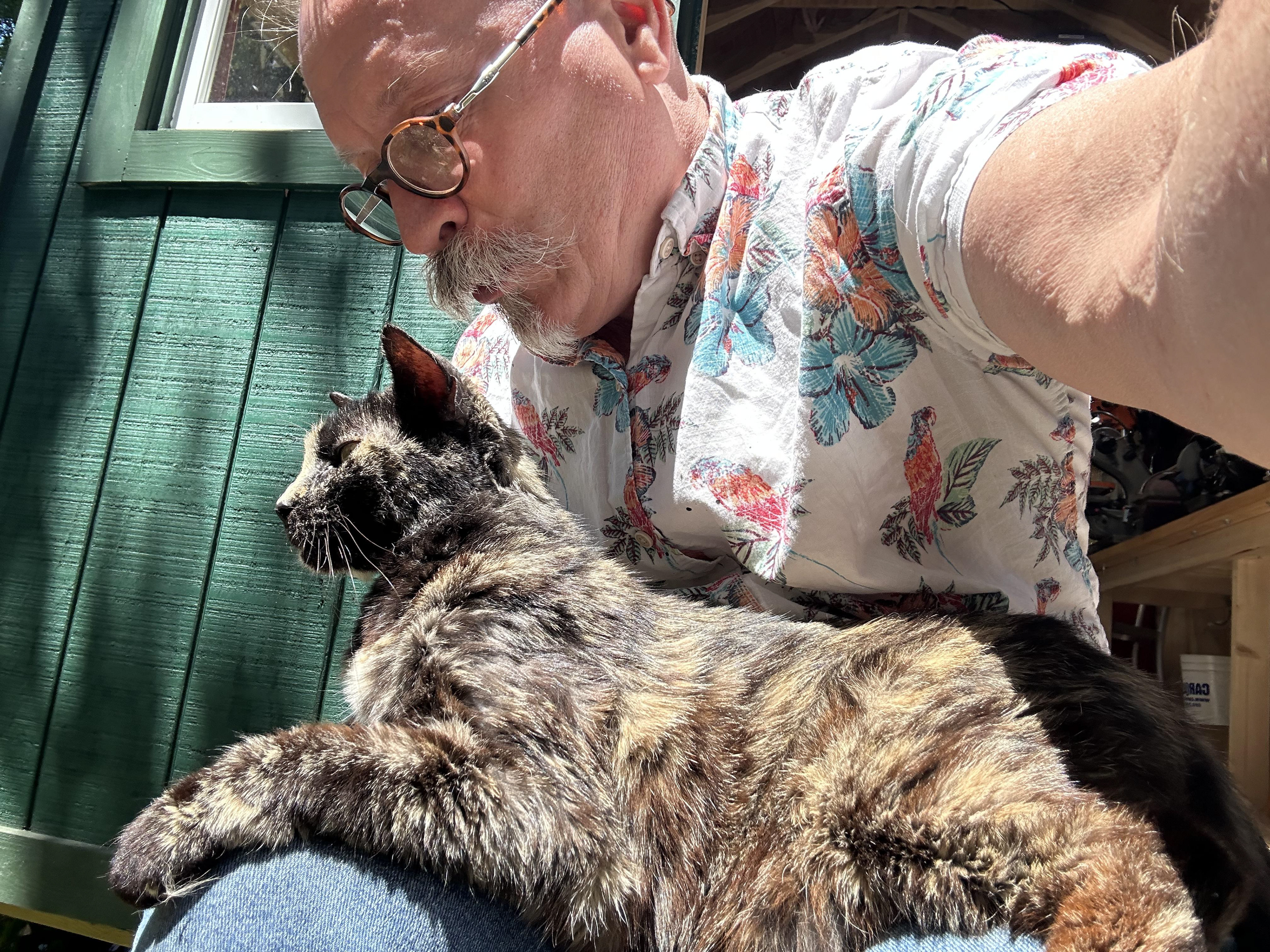
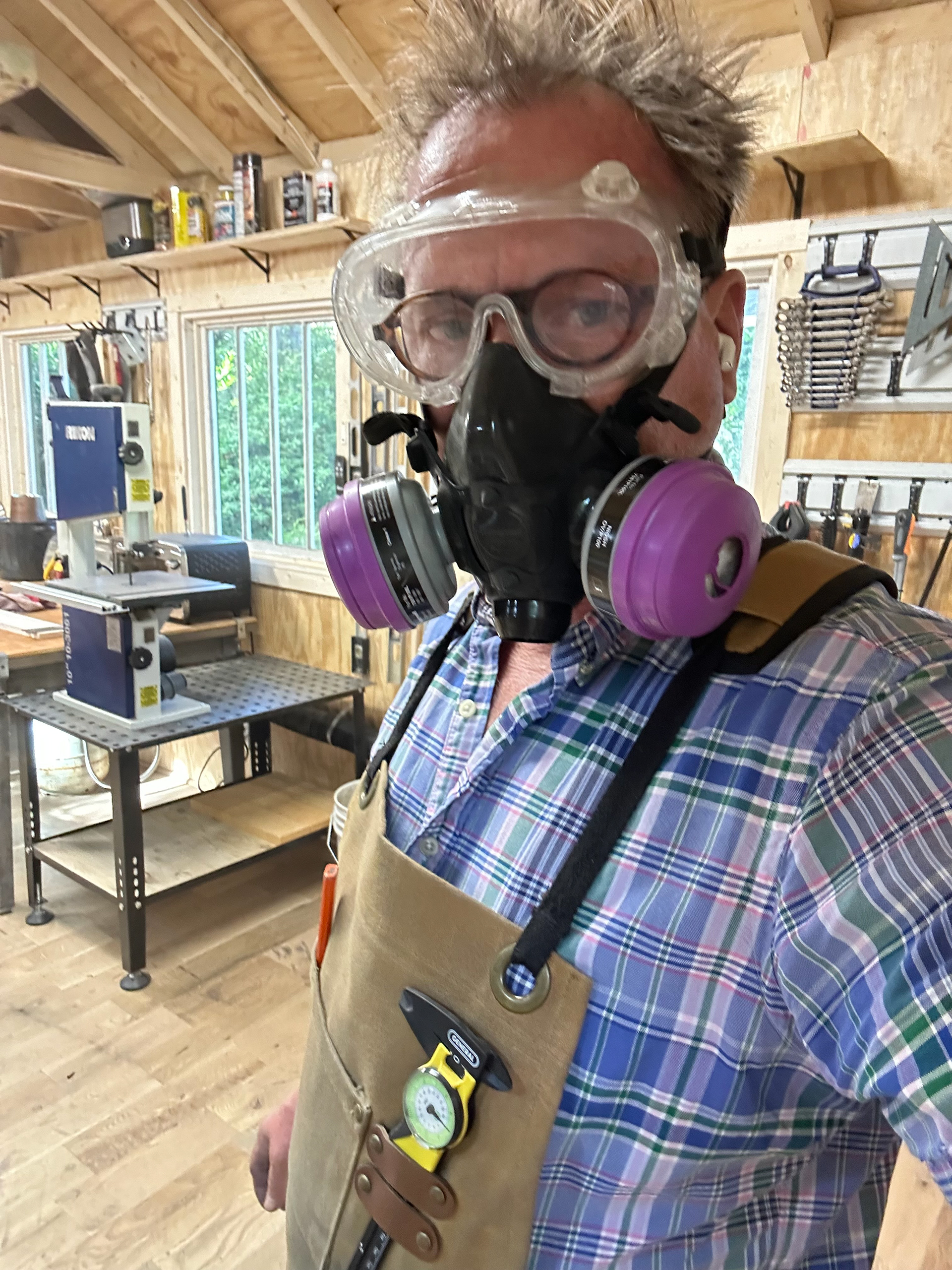
Safety First.
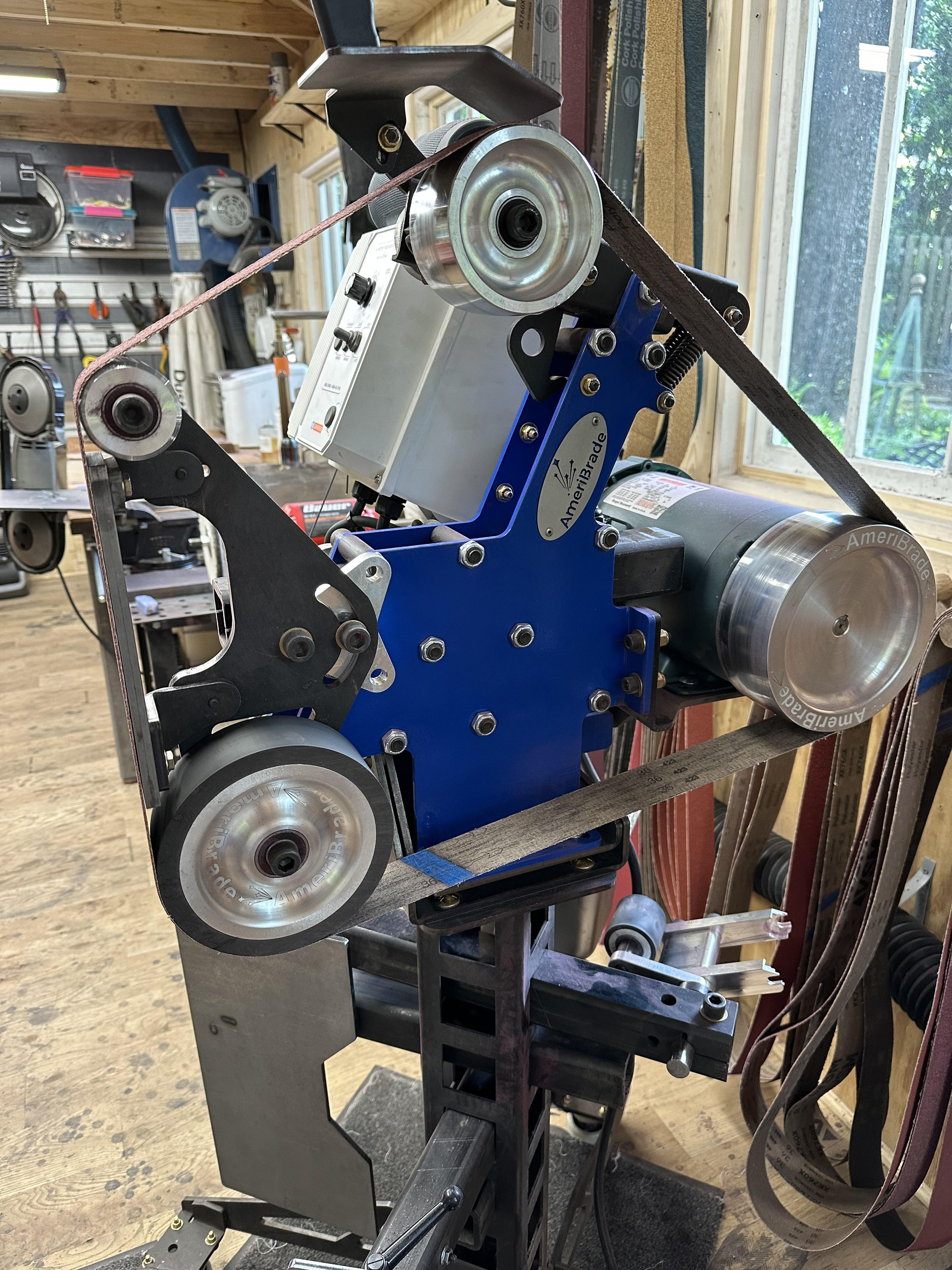
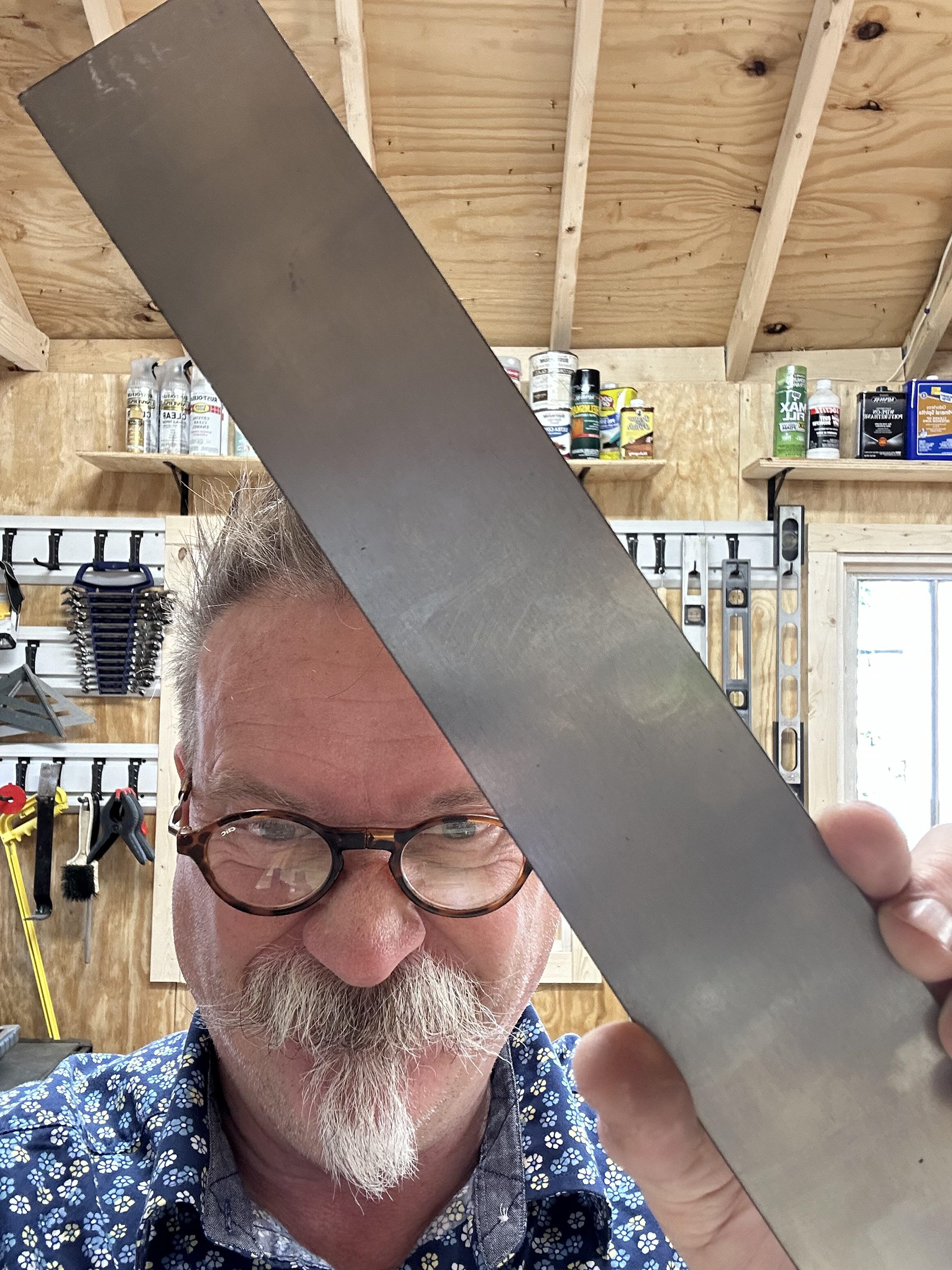
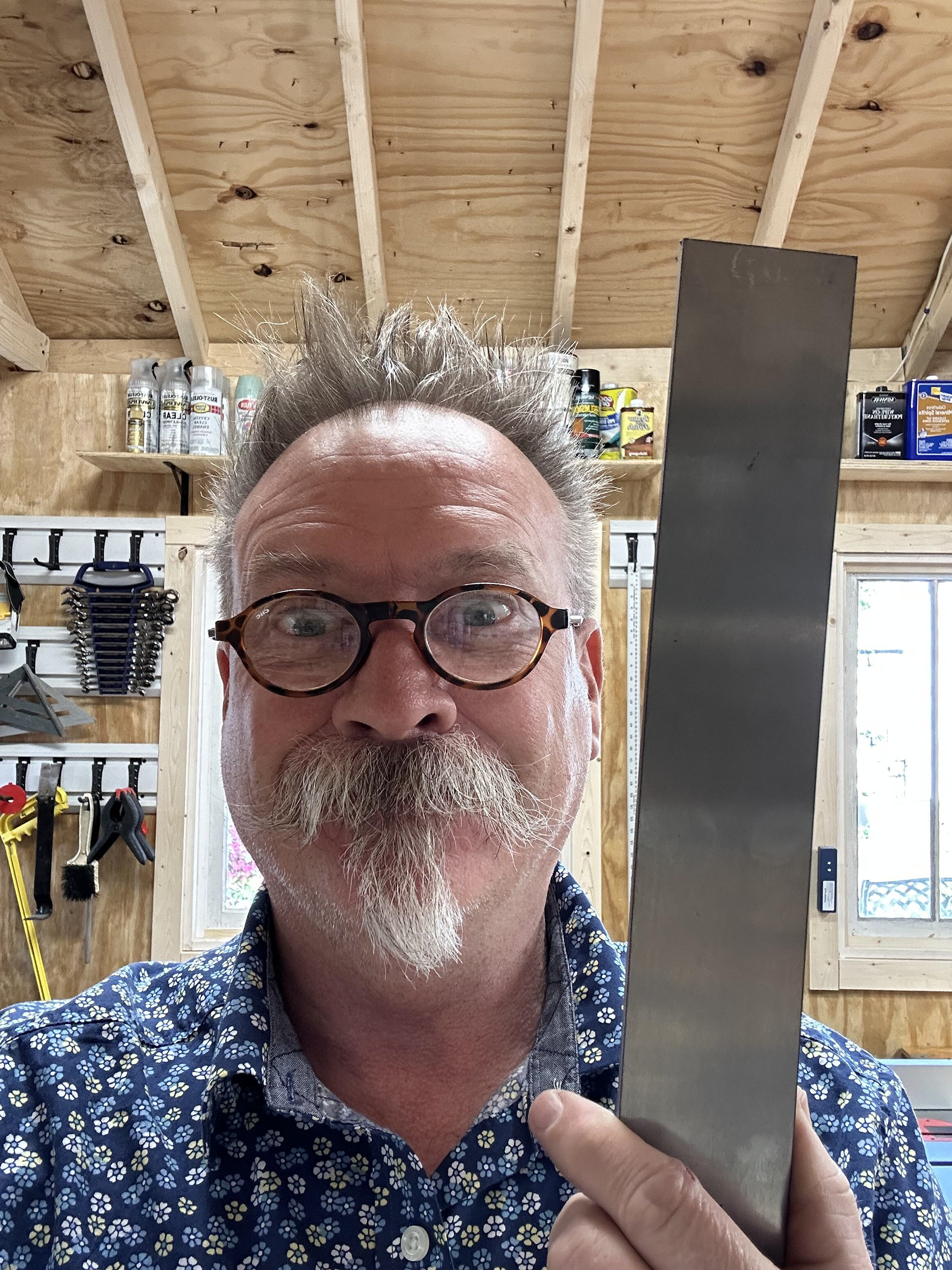
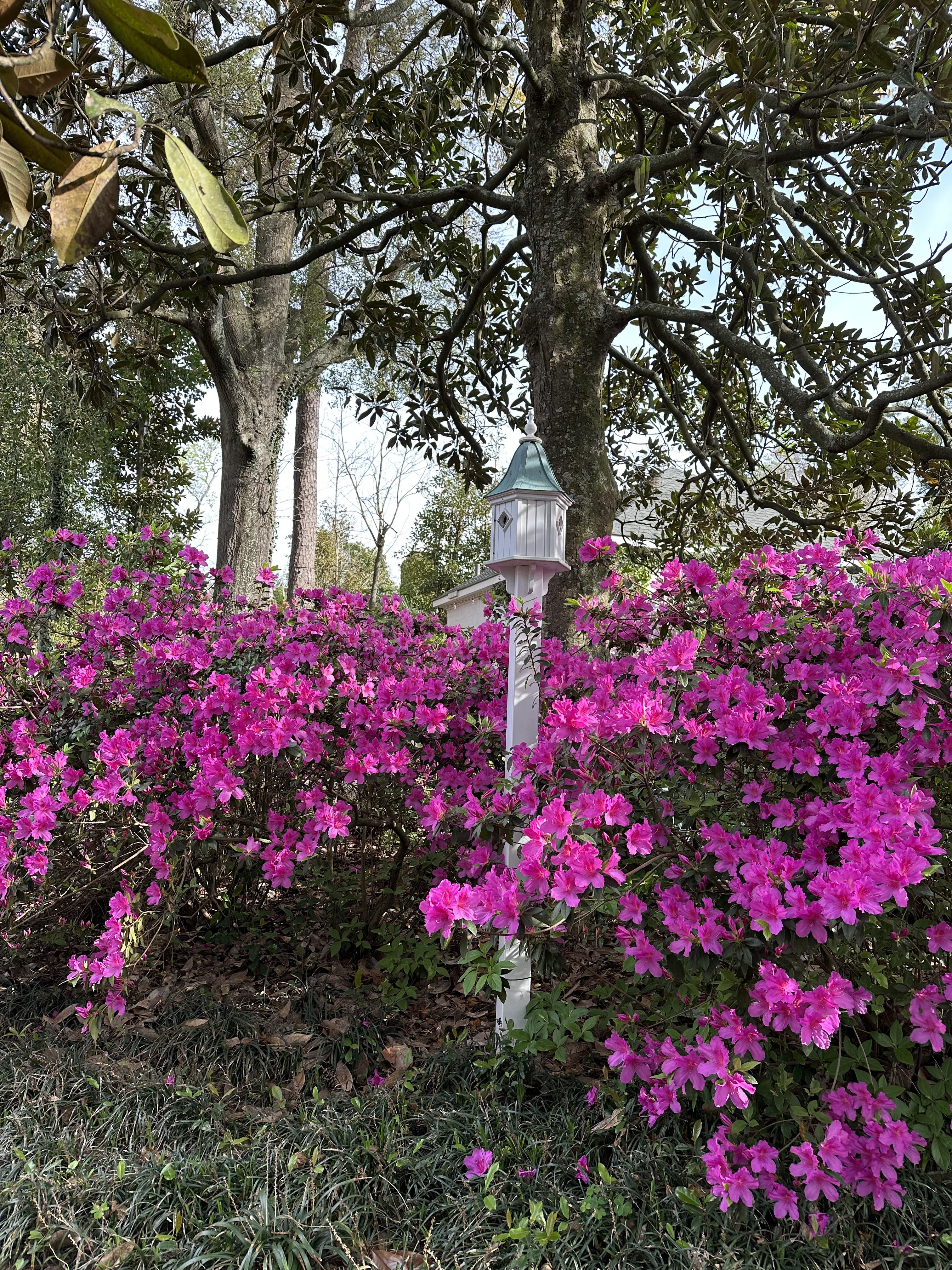
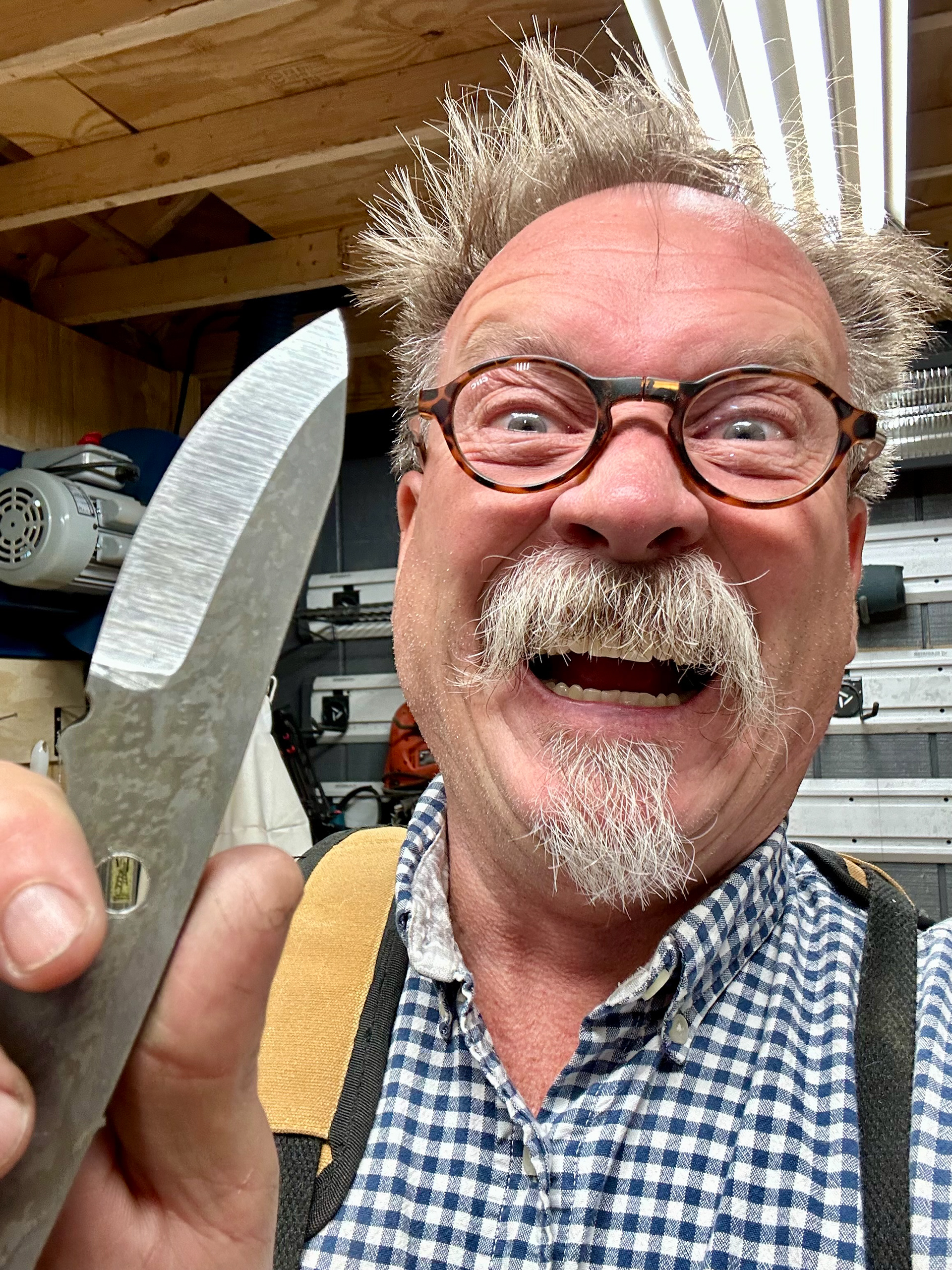
Daniel Ray Norris
FEBRUARY 8, 2025
FEBRUARY 8, 2025
The other day, somebody told me, "Daniel. I like your knives. They're nice looking. You must have a natural talent for making 'em."
And it got me thinking....
Aaaaand - I thought about it.
Making knives is about as natural for me as me trying to be a ballerina. It's difficult. It does not come easy. I don't have an in-born talent for it. It's like swimming against a strong current. It's a struggle. But I like it. And I like looking at the results of my struggle. [Insert joke about me in a tutu here.]
I was born and live in Wilmington, NC with my wife Mary and son Jack. I teach Biology at Cape Fear Community College full time and I design and publish books when I am not making knives or napping with my cat Roscoe.
My jobs and life find me at the computer a lot. Knife making has let me work with my hands in a therapeutic way. I have seen some blood, scars and deep gouges. And epoxy! - God have mercy the epoxy (and dust) gets everywhere. I do have to say it is a completely dirty endeavor. I have never been so dirty all the time! My hands and finger nails are always grubby and grungy looking. But it's been worth it. And it's been fun. I'm just a third grader in the hierarchy of knife making. My advice: Get off the computer or the phone and make something with your hands.
My first knife was pitiful. It was an abject failure. Very slowly I made my way towards crafting a decent knife that I would not be ashamed of. A few mild successes buttressed my bruised ego and I began to think I might eventually get there. Knives #8 and #9 gave me hope. And then I hit a brick wall. So many failures.... I came to the conclusion that I was being too cautious when grinding bevels. I’d go through the process of angle-grinding a 2" by 12" slab of 1095 steel (on a Jet 2x42 grinder) and then at the belt grinder I would go almost catatonic. The scraggly shard that barely looked like a knife was staring at me. It didn’t want me to go any further - or so I thought. I had worked hard to give it form. I didn't want to make a mistake grinding it to become a knife. I had to get around this mental block. I thought about it for a while and came up with an idea. Like a kid on the high diving board, I had to just psyche myself out and jump into the pool - I had to grind with mad abandon. Damn the torpedoes - full speed ahead! Well, I did just that and I found I was able to get a good bevel when I was “loose in the brain” like this. Reasonably nice looking knives did finally begin to emerge from my knife shop. And this was especially true when I got a proper grinder - a 2x72 from Ameribrade. They make good stuff.
(August-October 2023 - UPDATE: I bought an EvenHeat LB 22.5 heat treat oven. Much reduced scale issues and forge marks. I am now working exclusively in stainless steels - mainly AEB-L)
My work is certainly not comparable to a more seasoned knife maker's work. But I do have knives for sale and they really aren't that expensive. My earlier knives have a bit of forge scale, stray marks and dings from production but I think it gives them character. My style is still evolving but lately I have found what I consider my look for this craft. I truly never intended to sell any of my knives. As a matter of fact - it was my original intention to keep them all - not unlike "The Mad Potter of Mississippi" George E. Ohr. He didn't sell all that many of his works but he was happy just keeping his "mud babies" to himself. I think there's a kernel of honor in that.
The names for many of my knives were mostly dreamed up by my wife. She has a tiny head but a really big brain. Got any advice or questions? Hit me up on the Contact page.
Daniel Ray Norris
Norris Knives, Wilmington, NC
Norris Knives, Wilmington, NC